Home / All / Quality Questions /
How does YADA's Quality Assurance (QA) and Quality Control (QC) teams perform their daily work?
How does YADA's Quality Assurance (QA) and Quality Control (QC) teams perform their daily work?
YADA's QA (Quality Assurance) and QC (Quality Control) teams work in a rigorous and meticulous process to ensure that every aspect of a product, from raw materials and packaging to the final product, meets quality standards.
YADA's QC team carries out rigorous inspections of each batch of raw materials, the final product and packaging materials.
Raw material quality and quantity inspection: Our team conducts product quantity counts to ensure that overflow short-packs do not exceed 3% and that moisture content is controlled within 12%. At the same time, we will carry out inspection according to the company's quality standard, take photos to record the records, and fill in the raw material inspection form to ensure the quality and quantity of raw materials.
Packaging Material Inspection: We carry out normal inspection based on GB/T2828.1 standard with one sample to ensure the quality and conformity of packaging materials. This process involves random sampling of packaging materials and exhaustive inspection to ensure that they meet our quality requirements.
Quality and quantity inspection of auxiliary materials: We check the surface/bottom of the carton for any obvious appearance defects such as dirt, breakage, crease, moisture, adhesive degumming, peeling layer, obvious color spots, unclear/wrong printing, etc. We also check the quality and quantity of the raw materials according to the company's quality standard, and take photos and records. At the same time, make sure the carton barcode can be read out clearly, no error, and carton size (length, width, height) up and down error shall not be more than 2mm. for the same batch of big goods color should be consistent, there are damaged or open box should be picked out, layout printing content should be consistent with the scheduling requirements, there are errors need to be consistent with the production requirements. Layout printing content should be consistent with the production requirements, there are errors need to be picked out.
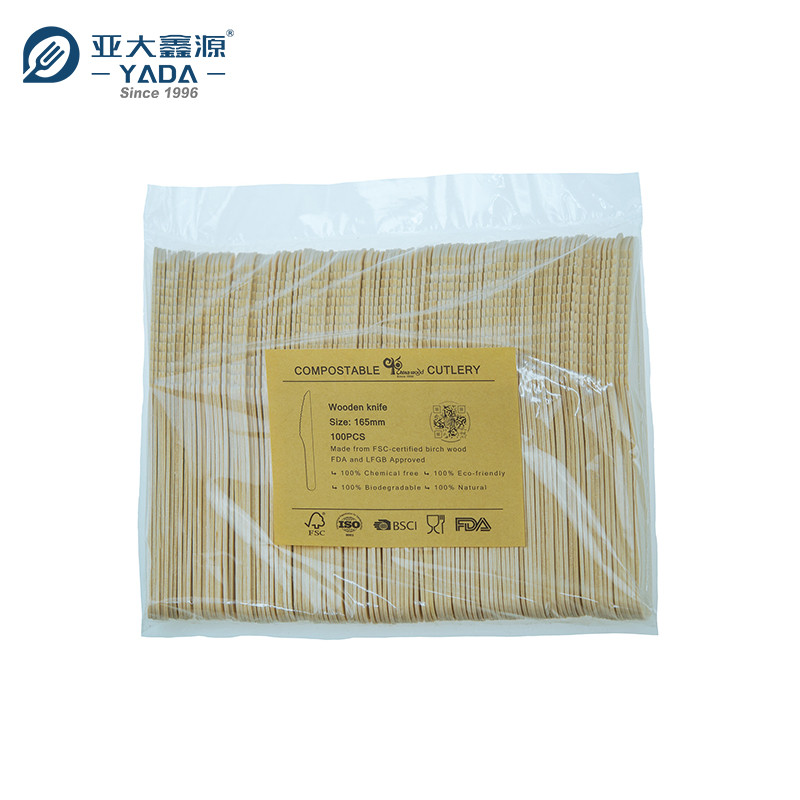
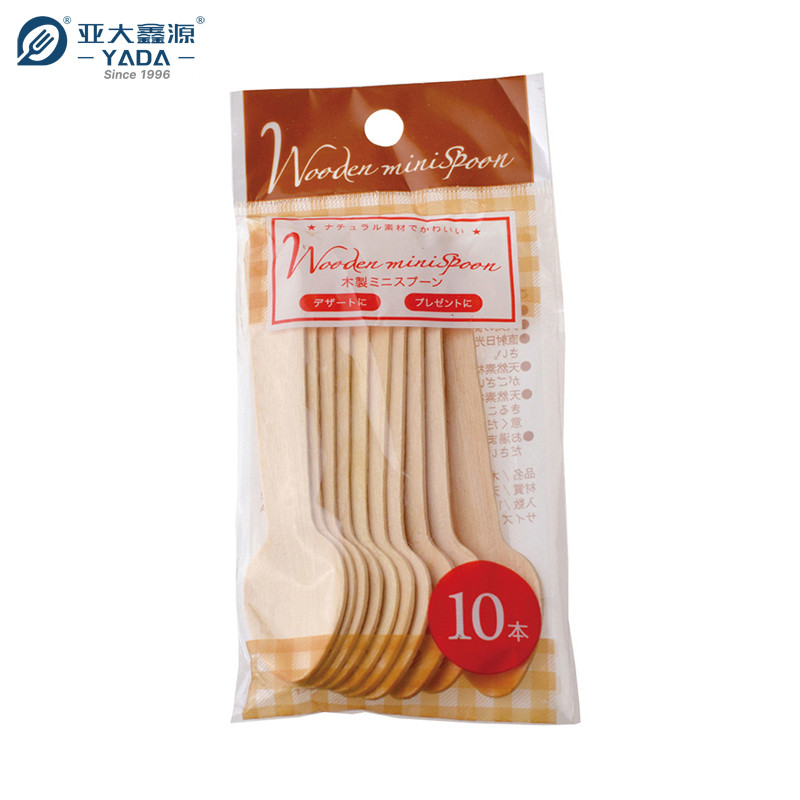
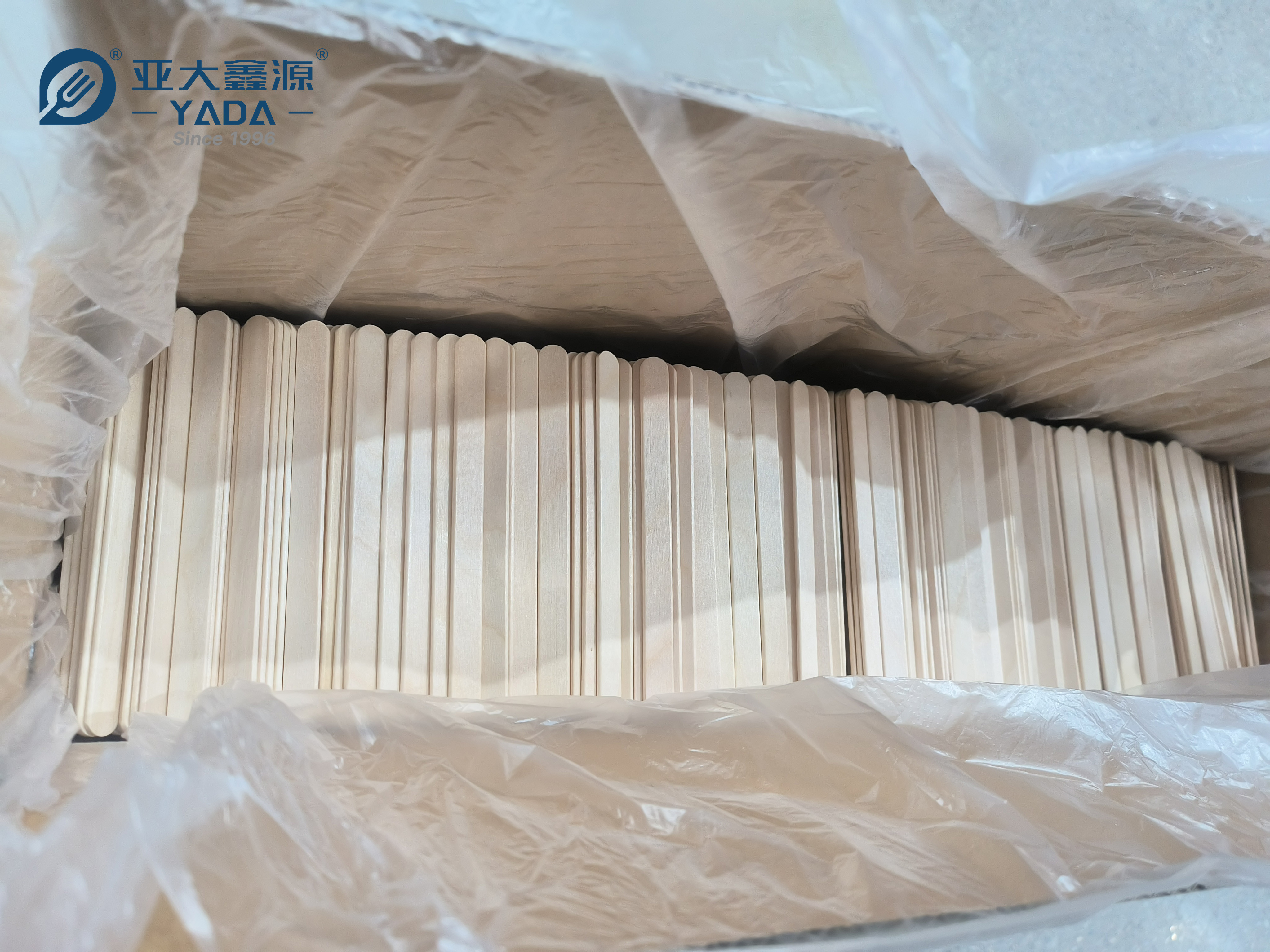
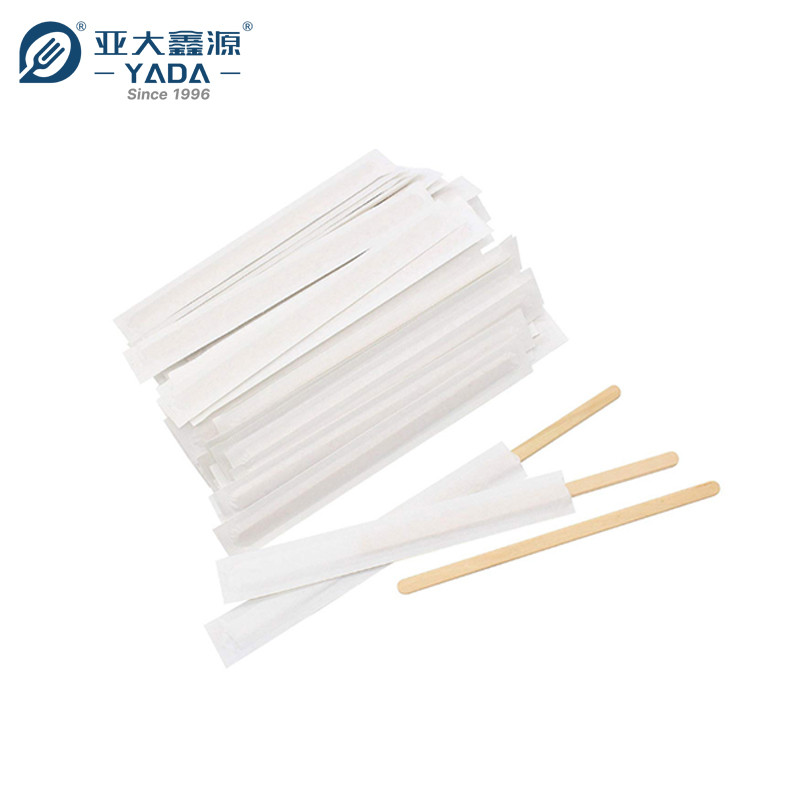
Plastic bag material inspection: we ensure that the plastic bag material meets the scheduling requirements, if there is color printing, then pay attention to the printing content, color and scheduling requirements. The quantity should be counted and consistent with the purchased quantity.
Carton inspection: the layout of the text printing should be correct, consistent with the scheduling requirements (except no printing). Quantity should be all counted, in line with the scheduling requirements, the color has special requirements to pay special attention. Carton positive mark mark should be consistent with the sales sample issued by the same, font printing is good, can be identified, carton number should be error-free, neatly written, there should be no damage, crease / dent, moisture and other undesirable phenomena, paste sealing should be uniform in place, not upward.
Requirements for packing tape.
If there is no requirement, there is no need for packing tape. The appearance of the outer box should not be deformed. The inner packaging of the outer box or middle box should be in line with the customer's requirements, placed in the same direction, with anti-scratch cardboard placed on top.
Judgment and record: We make judgment on the inspection results, which include qualified, returned, picked, special, reworked and scrapped, and fill in the inspection form for filing. These records will serve as important evidence of quality control for future traceability and continuous improvement.
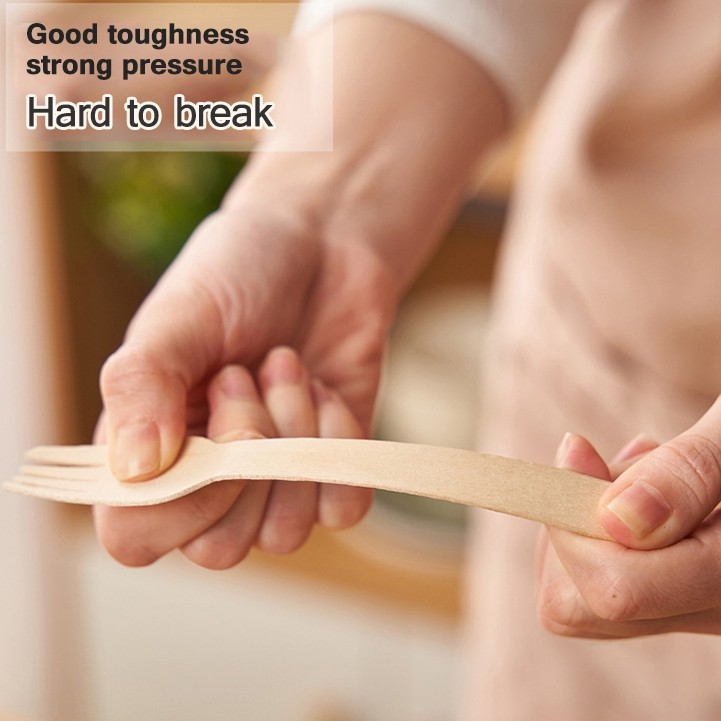
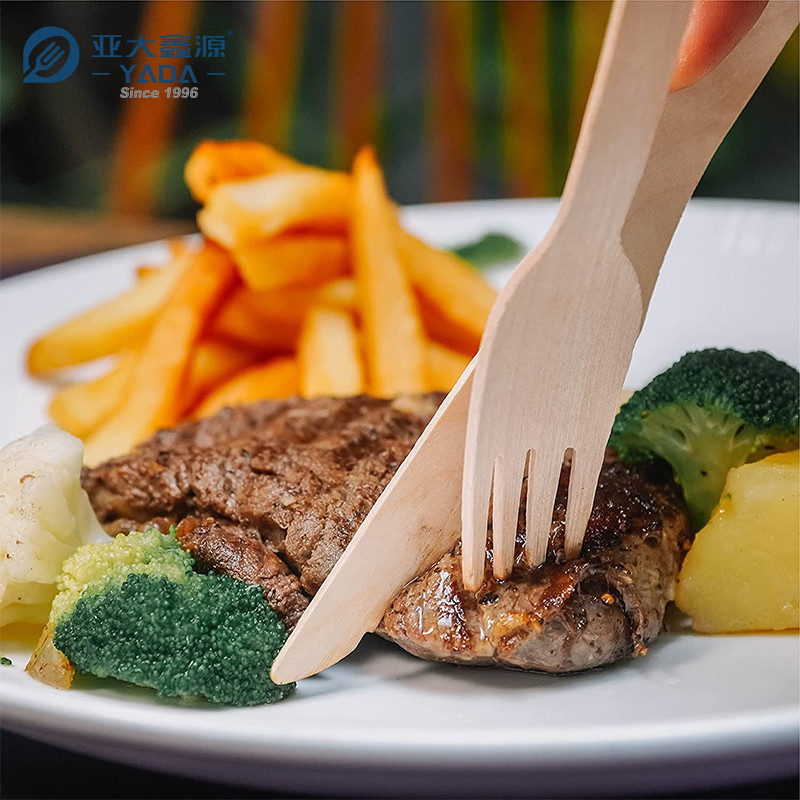
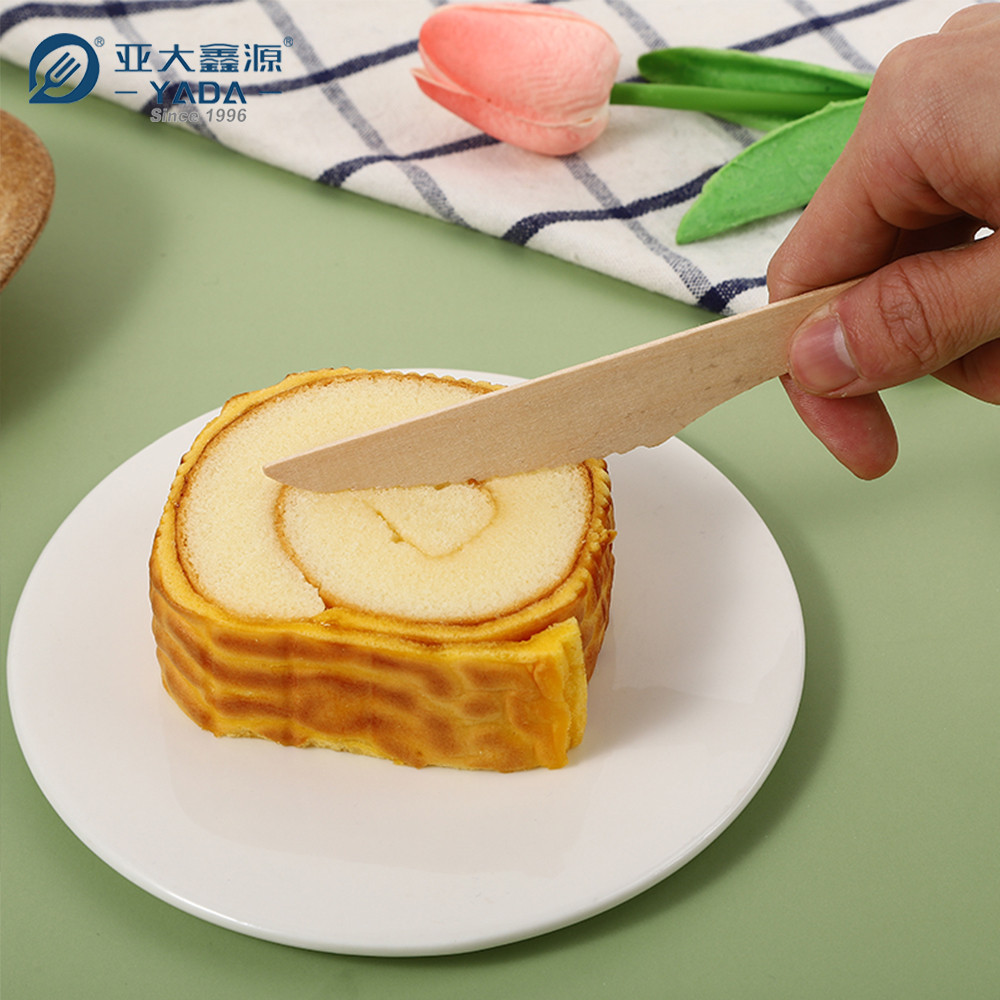
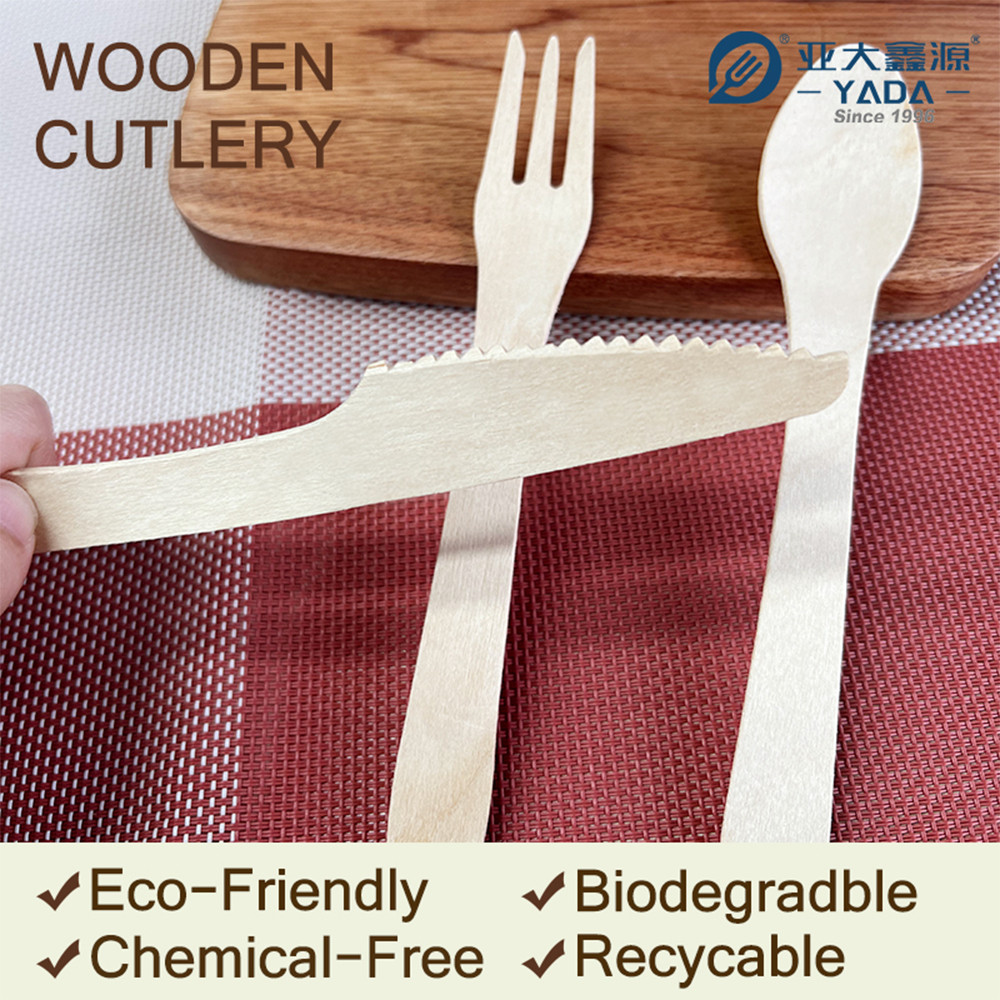
When conducting finished product inspection, sampling is usually done by fixed number sampling, i.e., a certain number of samples are randomly selected from a batch of products for inspection.
Outer box mark / appearance check. Verify whether the outer box mark mark is consistent with the sample issued by the sales, to ensure that the font printing is clear and recognizable. Check whether the writing of the carton number is neat and error-free, no damage, folding / dents, moisture and other bad phenomenon. Seal the carton in a standardized way, with even sealing in place and no upward movement. Decide whether packing tape is needed according to the requirements, and do not use packing tape when there is no specific requirement. The appearance of the outer box shall not be deformed.
Open the outer box and take out the middle package. Check whether the packaging in the outer box or the middle box meets the customer's requirements, and the direction of placement should be consistent. Anti-scratch cardboard should be placed on the top, and the number of packages should be referred to the text description of the mark. The appearance of the package shall not be deformed.
Take out the carton and check the appearance of carton. Check whether the surface/bottom of the carton is obviously dirty, broken, creased, wet, glued off, peeled layer, obvious color spots and other appearance defects, to ensure that the carton bar code is clear and readable, no errors
Open the carton/center pack and check the inside. Check cartons and other plasticized products to ensure that the labels are correctly affixed.
Product quantity and quality inspection, product quantity overflow short packs not more than 3%, moisture content within 12%. According to the product quality standards, the product appearance, length, diameter, form, etc. were inspected.
When carrying out finished product inspection, the following points also need to be noted:
Keep the calibration and maintenance of inspection equipment to ensure the accuracy of measurement. Train professional inspectors to improve the accuracy and efficiency of inspection. Record detailed inspection data for traceability and continuous improvement.
Feedback inspection results to the production department in time to solve quality problems together. Through these measures, product quality can be effectively controlled and improved to meet or even exceed customer expectations.
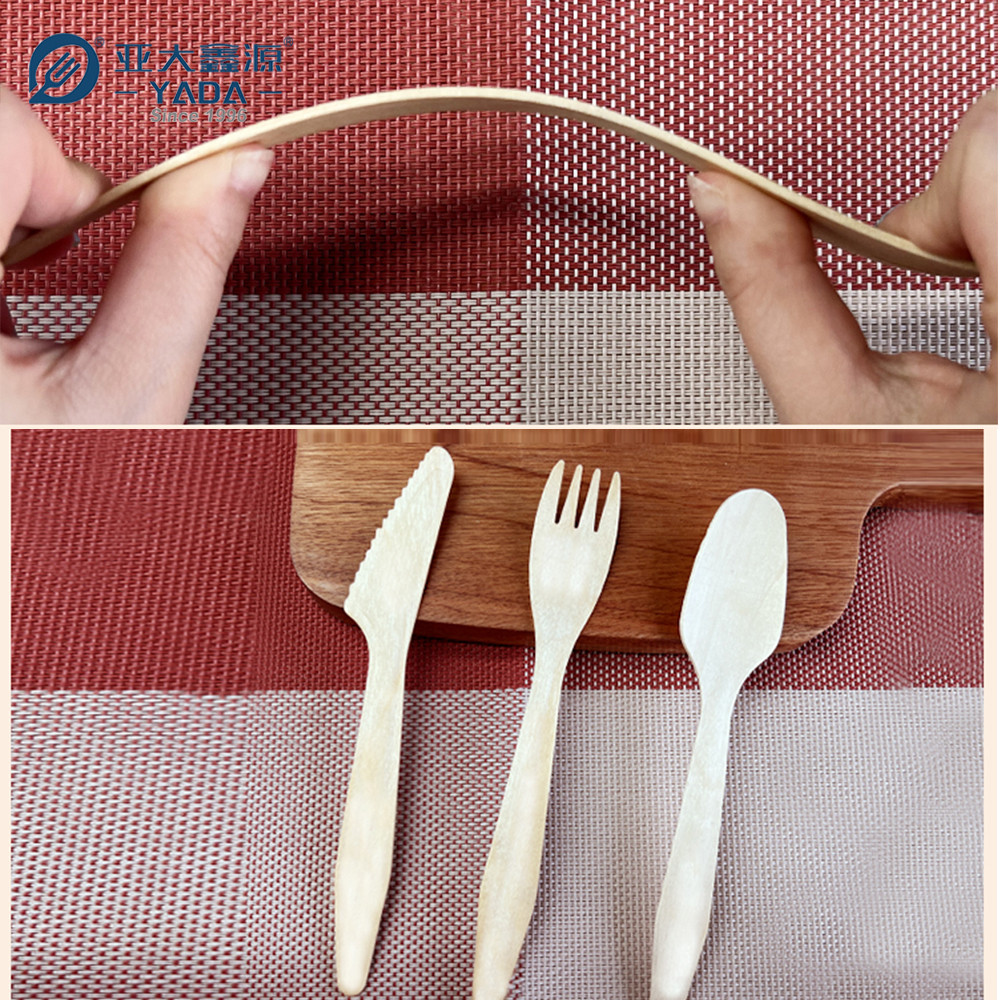